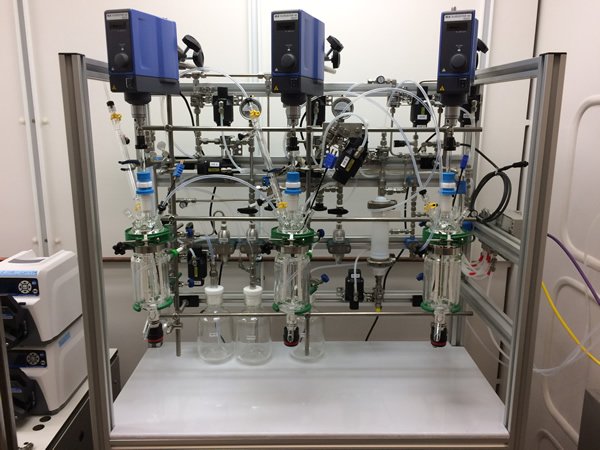
Continuous vs Batch
Typical drivers for choosing continuous instead of batch reaction are fast kinetics, highly exothermic heat of reaction, or hazardous reagents. However there are several things to look for in the batch reaction to cause one to think about continuous. Many of these are quality and cost drivers in addition to safety.
If the answer to any of the following questions regarding an existing batch reaction is yes, then it may be a good candidate to convert from batch to continuous.
Is the yield or impurity profile sensitive to reaction time, in other words are there significant late forming impurities?
Is the product unstable to end of reaction conditions?
Is the yield or impurity profile sensitive to mixing rate?
Is the yield or impurity profile sensitive to heat-up rate or cool-down rate?
Does the reaction use a heterogeneous catalyst that does not have a metal leaching issue? (In this case, there could be an advantage to continuous fixed catalyst bed PFR.)
Does the yield or impurity profile benefit from instantaneous all at once mixing of the two coupling reagents?
Is there a lag time or delayed catalyst initiation time in the batch reactor? (In this case, the advantage of continuous is that the reaction is always “on”.)
Is the best reaction temperature outside the normal range of typical existing batch reactors? (>120 C or <-20 C)?
Is the required throughput higher than can be achieved with the existing batch infrastructure?
Is the product cytotoxic, which would lead to advantage of using a small portable inexpensive ‘disposable’ reactor dedicated to that product only?
Is loss of material a higher than normal risk in the event of batch operational issues? (In this case, the advantage of continuous is that there is less material at risk in the reactor at any given time.)